|
|
Posted by oxric on
08-26-2011
|
fiogf49gjkf0d Hi everyone,
It is quite ironic that the day I hear from Fane telling me that the Fane 8Ms are finally ready, I should receive this update from my horn maker maestro. Russ Collinson of Layers of Beauty. Russ, if you ever read this here, please take a deep bow. Russ has been a real tower of strength not only putting up with one million questions, slight changes to the original designs, thinking about future requirements and ready to accomodate my most far-fetched notions with never a single complaint but a very welcome dose of reality where required.
This is obviously part of a bigger picture. The midrange 200Hz, 250Hz, 400Hz and 550Hz horns have been made in Germany and will be delivered shortly. In my room, I cannot accomodate the 200 Hz horns, and will need to choose between the 400Hz and 550Hz horns eventually, but at least now I have the possibility of trying different configurations in different locations instead of dreaming what they sound like. All these horns named above are tractrix but I also have a 322Hz Le Cleach which is however 55cm in diameter to play with.
The room for Le Horn is now ready except for lighting and storage for my LP/CD book collection which I would have commissioned from Russ if distance was not an issue. I normally try to keep equipment outside of the room and I have an adjoining cellar that can be used to this effect but I am not convinced this is the right solution given the use of tube amplification. The room itself acoustically is superb being part of a 5 centuries townhouse with 70cm thick exposed stone walls which present not a single pair of parallel sides.
There are issues, complications that I am already aware of and a host of other imponderables that will come to haunt this project but I am fortunate to have found help in sometimes the most unlikely of places. I have also had to accept disillusionment. I hoped somehow against all odds that a 50Hz horn would be a possibility but I must honestly say that in this room this will not work.
So what about the Upper bass horns? They are 96cm in diameter, the mouth opening given a very slight rollover and approximately 110cm in length including back chamber. They are designed to be accomodated in a frame that is infinitely adaptable to accept pretty much any horn of any size at any height that I can throw at it and which has provision to grow in height when I move to a room with higher ceilings eventually.
The aesthetics are chosen to suit the room and nobody's personal taste including mine. I would have had the horns all in black but my wife decided that the room which has dark pink mortar and stones would accomodate it better with dark red that would match a feature wall and the spirit of the region - we are after all in the heart of the 'Route des Vins' in one of the prettiest parts of France.
I should say thank you but it is too early for that and the end is still a long way off. As Bilbo said when he set off from home after the 13 dwarfs, " we do not know where the road outside our front door will lead ."
Best wishes from Ribeauville Rakesh
|
|
|
Posted by Romy the Cat on
08-26-2011
|
fiogf49gjkf0d As I understand they are 110-125Hz horns, they look fine to me. The thickness of mouth I would say a bit too thin but it is trade off as the give horn has no horizontal edge which is better acoustically even though loose slightly visually.
There is one more subject that most of the people are missing. I personally located horns not in-the-walls as most of people do but my horns are extended well into my room. I feel that this sounds way deferent but this is not the point. The point is that the back of the horn in my purely visual perspective might have some kind of termination accent. I do not like the flat line as everyone do and I would like to have some kind of balancing budge on the other side around the back chamber. This is from my perspective gives some kind of harmonizing completion if the enter horn, not to mention solidify and damps the back chamber. Below are a few pictures how the end budges looks like. I feel for a horn that sites in the mid of the room it looks sexier then the straight line ending.
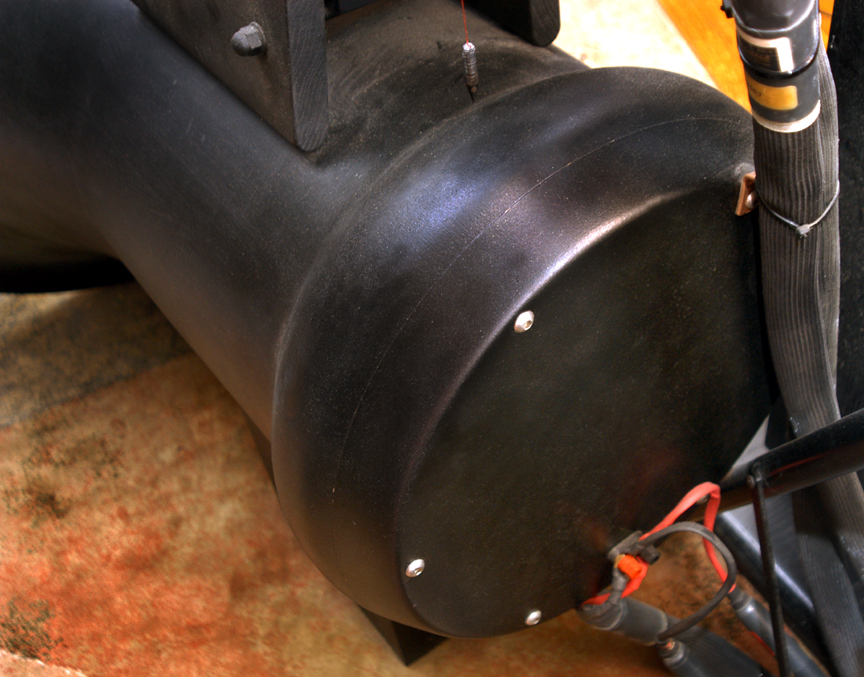
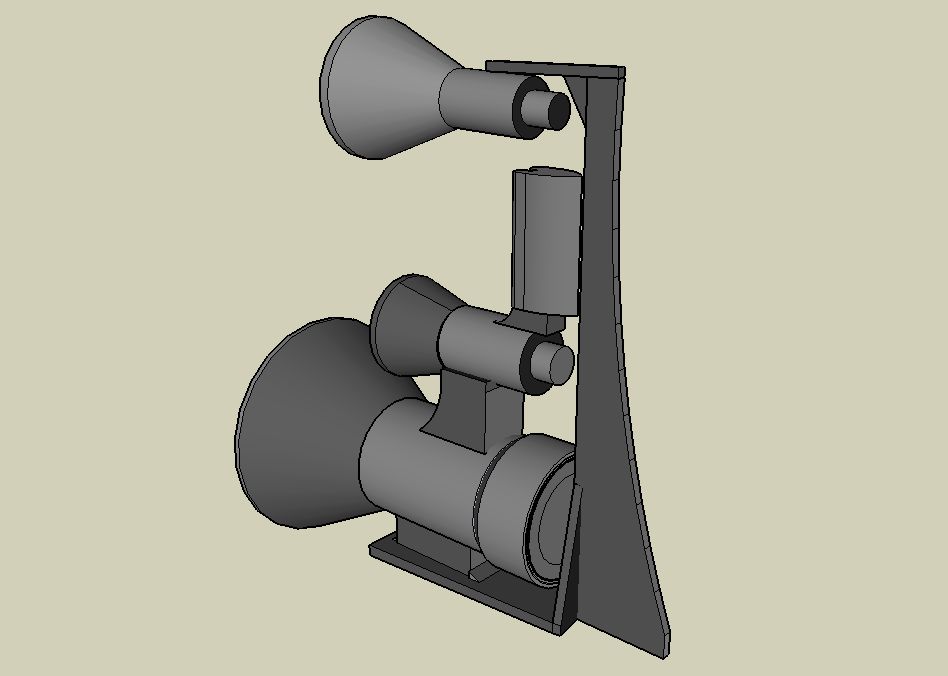
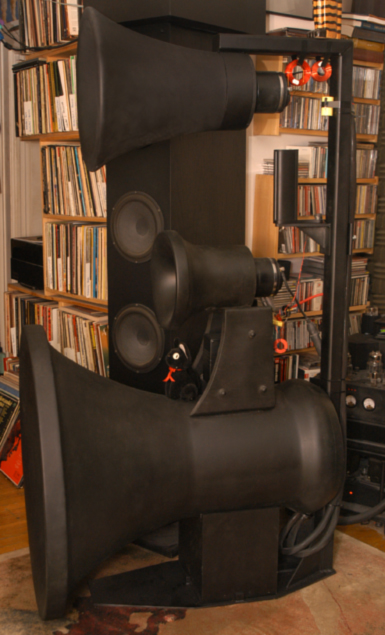
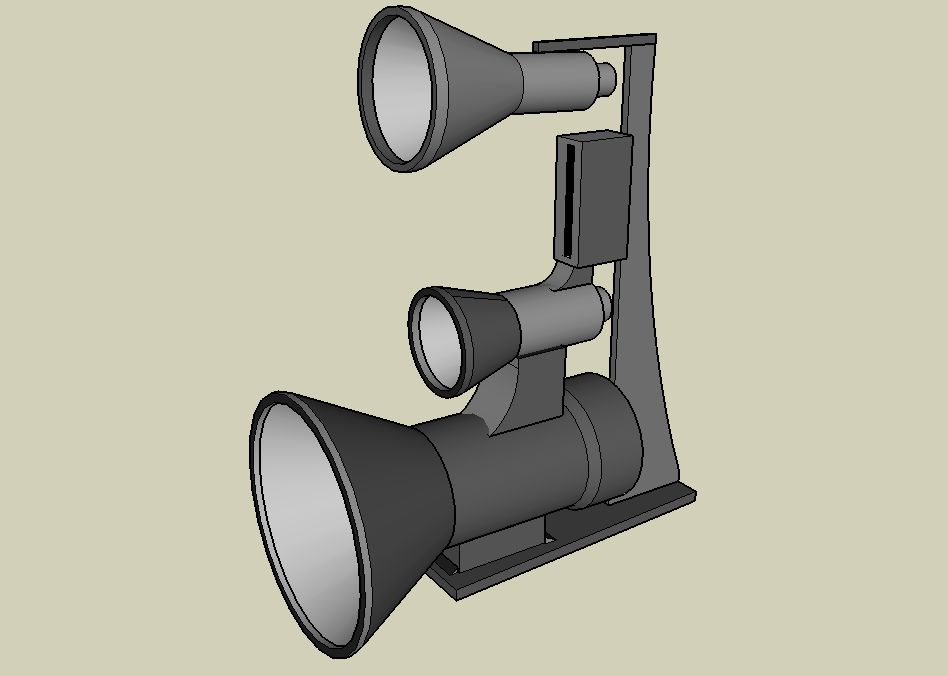
|
|
|
Posted by oxric on
08-26-2011
|
fiogf49gjkf0d Romy the Cat wrote: |
There is one more subject that most of the people are missing. I personally located horns not in-the-walls as most of people do but my horns are extended well into my room. I feel that this sounds way deferent but this is not the point. The point is that the back of the horn in my purely visual perspective might have some kind of termination accent. I do not like the flat line as everyone do and I would like to have some kind of balancing budge on the other side around the back chamber. This is from my perspective gives some kind of harmonizing completion if the enter horn, not to mention solidify and damps the back chamber. Below are a few pictures how the end budges looks like. I feel for a horn that sites in the mid of the room it looks sexier then the straight line ending.
|
|
Romy,
Good point.
This is actually exactly the subject of conversation I had earlier today with Russ but I was talking about 'accenting' the end of the midrange horns. For a long time I had considered having that bulge ending the 115Hz horns but for some reason mistakenly imagined in my mind that the back chamber was a cuboid design which was not a continuation of the horn but its natural and contrasting end. I like and maybe prefer the bulging back end and maybe that will better match with the bullet shape ends of the horns I will eventually have made to replace the ones I will be using to experiment for now.
Food for thought...
Best regards Rakesh
|
|
|
Posted by oxric on
08-26-2011
|
fiogf49gjkf0d
|
|
|
Posted by N-set on
09-03-2011
|
fiogf49gjkf0d It's too late for Rakesh, but I'd use MDF of various thickness, randomly interchanged to avoid repetetive structures.
|
|
|
Posted by scooter on
09-03-2011
|
fiogf49gjkf0d N-Set,
That is a really interesting point for designs going forward; one step further would be to vary different materials for each layer.
Microsoft Excel has an easy random number generator to automate the thickness calculations. Actually getting true random numbers out of a PC is difficult due to the core design of the processor but given the small number of laminates in this project, the Excel approximation should be fine.
Rakesh does get some of this benefit given that each layer is of a different size, the relatively random composition of each MDF slice, and that there is different bonding agents both within each MDF slice and between the different layers.
|
|
|
Posted by N-set on
09-03-2011
|
fiogf49gjkf0d There are quantum RNG's available, unbeaten by any classical RNG just by the physics of their operation, and you can have one for $200 or so ona PC card, but scooter I think that's way too much. Just randomly stacking several available thicknesses should be enough if this trick has any merit. Alternating material: I've also thought abut that but then dissmissed the idea.
|
|
|
Posted by Paul S on
09-03-2011
|
fiogf49gjkf0d I am too lazy to fish it out again, but someone did a nice study on room dimensions that might partially apply here. In this study case, the Golden Ratio was deemed sub-optimal in point of fact, which begs the question here, what is "random", in point of fact, except perspective. Practically speaking, even if "random" is the sonic ideal, it might work out just as well to use find-able thicknesses and varying adhesives in a +/- random sequence, then play with "surface" treatments. I will say that these horns "look thin" to me, except what the hell do I know, and what matters is how they sound in the end, anyway. I also don't know about the driver choices... But all this is part of the insanity of building serious horns, and there's probably no way around it.
Best regards, Paul S
|
|
|
Posted by Romy the Cat on
09-03-2011
|
fiogf49gjkf0d
scooter wrote: | That is a really interesting point for designs going forward... |
|
I would very much argue that it is interesting point. Not because it not interesting but to highlight the fact that this interesting point has no practical answer.
First of all in the case of Rakesh horn what N-Set proposed is not necessary. Those 115Hz Hasqiun-style horns that Rakesh emulates are well dumped with own mass and own construction techniques – layers of particles boards with lagers of proper glue are great damping environment. In addition it is juts 100Hz – not too stressful foe the horn of this design. When and if Rakesh goes for his 50Hz horn it will be much different story – in there firmness of the assembly will be much flimsier for the frequency it cares and to use randomly interchanged damping and randomly interchanged thickness will effective.
Why in such case I would argue the rational of this approach? In particularly why would I argue it if I myself used the very same approach in construction of my own 42Hz horn? The answer is that all logic that we use is purely intellectual self-gratification. Sure we can measure the resonances in mouth but we have no mechanism to evaluate how different degree of resonances and different randomness of mass distribution in reality affect Sound.
In addition, in case of 50Hz horn there are zillion OTHER reasons why the horn sound in one way or another. How to subtract from those zillion reasons the contribution of random masses? I do not know the answer.
The problem is complicated further by the fact that the people who built many horn and try different construction methods also not able to say truths because of various reasons. It is just too complex, too expensive to investigate and in most cases not necessary or needed to wide public, therefore not worthy to invest for horn builders.
So, my attitude is following. I build my 42Hz horn and I exposed all my techniques I used. In the very end I do like how it sound but I would not name a single specific technique that I feel is responsible for the sound that I like. Furthermore, if my horn was used in playback differently then I might be less (or more) satisfied with how it sound. So, looking back to my midbass horn project I might call myself an experienced guy (it took 10 year of thinking about that horn) but do I feel that my experience give me option to say definitely about this or that construction techniques as an assurance of proper midbass sound. I do not feel this way and therefore I would argue any certainty in large horn construction.
I have seen a lot in audio. I have seen amazingly sounding bass enclosures made with over-damped and under-damped boxes. I have seen (even owned) insanely expensive enclosure what the microscopic resonances were measured by laser readers and the enclosures still sounded like shit. I have seen the enclosures made from thin horrible wood with firmness of cardboard box and some of them had phenomenally interesting bass. I feel that there are no rules and there are no winning patters. It is very complex to foresee anything in bass resonance and I feel that empirical practicing, observing own very specific results, proper interpretation of results and then to react upon those results is the only way to accomplish Sound of own envision. I am not even mentioning that what a person envisions is a reflection of his various non-audio qualifications, but it is a while deferent subject….
Rgs, Romy
|
|
|
Posted by oxric on
09-03-2011
|
fiogf49gjkf0d Romy the Cat wrote: |
...this interesting point has no practical answer. First of all in the case of Rakesh horn what N-Set proposed is not necessary. Those 115Hz Hasqiun-style horns that Rakesh emulates are well dumped with own mass and own construction techniques – layers of particles boards with lagers of proper glue are great damping environment. In addition it is juts 100Hz – not too stressful foe the horn of this design. Rgs, Romy
|
|
When I obtained the spreadsheet of measurements for my 115Hz, a number of possibilities presented themselves to me, all of which were easily achievable. I could easily use alternating layers of plywood and in fact had set aside some outrageously expensive 'panzer holz' to this end (see http://www.ltlewis.co.uk/), vary thicknesses of different layers and become more anal about the throat driver interface. In the end I did absolutely nothing. I was worried about the thickness and made sure that at the throat area the horn was about 160mm in thickness and this decreases to 70mm at its minimum. Why was I happy to have the thinning at the mouth end? I did not want to give any flat surfaces where the exiting waves would reflect in a uniform fashion. I would say that any modern horn, irrespective of aesthetics considerations, should have this feature.
It is interesting that Romy mentions '115 Hasquin-style horns' that I emulate since I did indeed approach John Hasquin to see if he could undertake this project (he would not) and for advice (which he is very generous with).
John Hasquin wrote the following in response to a query I sent him and it is well worth quoting in full:
"Re: Tractrix with Lecleach The mouth termination on the Lecleach helps to prevent defraction. This too can be avoided with the tractirx by high passing at slightly above the Fc of the horn. If you have the extra room you can use the Lecleach if you want, I didn't noticed any sound quality differecnes between the two for mid bass use. There is nothing to be gained from using other materials for the back chamber if you make it thick enough. My back chambers are 1.5 inches thick, so they are plenty stong. Using a denser material will only make an already heavy horn heavier. You can use any material you want. I like MDF because it is well dampened when layered and glued together. It is also not as expensive as plywood, or natrual woods. The AK151 should be good up to around 800Hz without too much trouble. They don't quite have the speed and snap that the Fane Studio 8M, but they are can be used. That's a decision you have to make for yourself. "
Horn lore is incremental. I agreed with most of that advice. In fact, the wall thickness of the back chambers of my UB115s are 10cm, i.e. close to 300% as thick as per JH's recommendation, based in part on what I know of the pressure that develops in the back chamber. I discarded the idea of experimenting with the AK151s in that horn based on what JH and a friend of mine in Paris told me about these drivers. I also had a look at Jeffrey Jackson's horns which are based on a slightly different approach to that recommended by JH but still does not use a full Lecleach profile. I was puzzled by this and Jean Michel Le Cléac’h confirmed that the profile is a truncated Le Cleach:
Jean Michel Le Cléac’h wrote:
Hello, The 140Hz horn commercialized by Eleven Horn is for sure a (T=0.707 )Le Cléac’h horn but the mouth is shorten and its roll back is quite small. This has surely been done by Jeffrey Jackson in order to have a smaller width than the complete roll back horn. See attached graph. Best regards from Paris, France
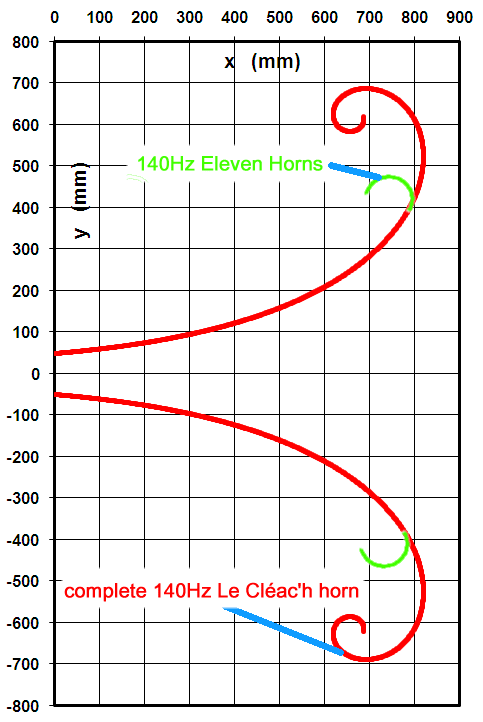
Since as JMLC himself makes clear, his calculations in themselves do not propose a re-evaluation of horn theory, but propose some advantages which mainly result from the minimisation of re-entry at the mouth, I decided to give the UB115s some of the theoretical benefits of the mouth design of a Le Cleach profile, without the concomitant increase in overall diameter of the horns, which I had set at an absolute maximum of 96cm (+ 27.3cm /2, i.e. radius of my 396Hz horns=109.5cm, with my LeCleach rollover, not more than 115cm, or + 21cm/2, i.e. radius of 550Hz horns=106.5cm
Romy the Cat wrote: |
The answer is that all logic that we use is purely intellectual self-gratification. Sure we can measure the resonances in mouth but we have no mechanism to evaluate how different degree of resonances and different randomness of mass distribution in reality affect Sound.In addition, in case of 50Hz horn there are zillion OTHER reasons why the horn sound in one way or another. How to subtract from those zillion reasons the contribution of random masses? I do not know the answer. The problem is complicated further by the fact that the people who built many horn and try different construction methods also not able to say truths because of various reasons. It is just too complex, too expensive to investigate and in most cases not necessary or needed to wide public, therefore not worthy to invest for horn builders. So, my attitude is following. I build my 42Hz horn and I exposed all my techniques I used. In the very end I do like how it sound but I would not name a single specific technique that I feel is responsible for the sound that I like. Furthermore, if my horn was used in playback differently then I might be less (or more) satisfied with how it sound. So, looking back to my midbass horn project I might call myself an experienced guy (it took 10 year of thinking about that horn) but do I feel that my experience give me option to say definitely about this or that construction techniques as an assurance of proper midbass sound. I do not feel this way and therefore I would argue any certainty in large horn construction. I have seen a lot in audio. I have seen amazingly sounding bass enclosures made with over-damped and under-damped boxes. I have seen (even owned) insanely expensive enclosure what the microscopic resonances were measured by laser readers and the enclosures still sounded like shit. I have seen the enclosures made from thin horrible wood with firmness of cardboard box and some of them had phenomenally interesting bass. I feel that there are no rules and there are no winning patters. It is very complex to foresee anything in bass resonance and I feel that empirical practicing, observing own very specific results, proper interpretation of results and then to react upon those results is the only way to accomplish Sound of own envision. I am not even mentioning that what a person envisions is a reflection of his various non-audio qualifications, but it is a while deferent subject…. |
|
I faced exactly the same dilemna with regard to the construction techniques that would be used in the making of the UB115s. Counter-intuitively I opted to err on the side of doing too little rather than too much. Rather that interweaving different thicknesses of different materials, I decided to educate myself. I am humble enough to know that I may not be able to fault these horns using these specifications and I will be quite happy to live with these as they are. Aesthetically, I actually prefer the look of the mouth as I have designed them. They appear more elegant and refined, somewhat more ethereal for such bulky structures and they avoid the blockiness that I do not find appealing in other tractrix horns that I have seen. I agree with Romy that the beginning of the horns is not right but for very different reasons and my solution will be different, to suit my aesthetic sensibilities.
What lesson is there in my endeavour for those who are about to embark on the journey of building or commissioning someone to build their upper bass horns (from emails I receive I know quite a few people are considering taking the plunge when means, family or real estate allow)? In my opinion, the first thing is that you must get started! The more you think about it, the more you consider the theory and pros and cons of different ideas, the more you will get nowhere as those that I consider the practitioners in the field have such different opinions of what works best. And please please please keep your horns under 1m in diameter! If you have a family and your means are limited - as mine are- forget about horns and just book yourselves a nice holiday somehere nice as these horns are inevitably expensive if you are having them made. There is more gratification in knowing that my littles ones have had a wonderful break in such an amazingly beautiful place as I am now, than having my horn loaded system in operation.
Lastly but not least, Romy's site is a great place for insights in a system that is so far ahead that we might only want to emulate what he has achieved rather than discover our own personal solutions, but do not expect it to be helpful to beginners (which is how I class myself) in a practical manner. Romy's advice above is to approach a master of the art such as Jeffrey Jackson or John Hasquin. My advice is the precise opposite. This is too big a venture to hand over completely to someone who will make all the decisions and balancing of sometimes conflicting priorities for you. Try to do it yourself if you can or get someone to build it who will listen to your needs and your vision and then give it shape.
One very last thing if I may. I am not a hidden marketing agent for Russ Collinson, and I do not get a discount for singing his praise, although I fear Romy might think so, but he has been so exceptionally capable that one would not think that these were the first horns that he has ever built. But it was an amazing journey from the very beginning, from the time when he declined taking on this project, to the discussions that we had about the construction techniques, and it never failed to amaze me how he was open to new ideas, was prepared to look at what other people had done, and select what worked best in his mind, and develop and modify his own tooling where necessary. If you are in the UK or anywhere he can ship to, I would without hesitation say that you should give him some serious consideration.
Best regards Rakesh
|
|
|
Posted by oxric on
10-18-2011
|
fiogf49gjkf0d
I think it is time, today being both my birthday and the day when I received the first updates from Russ regarding the frames for my 'Rakeshorns' system, for an update.
The idea behind the frame was to have a construction that both provided a fair amount of flexibility and adaptability, a certain degree of modularity (so that the frame could be extended as required, within reason) and hopefully also achieve some degree of elegance in terms of overall esthetics.
A key functional requirement was the ability to make the cables less obtrusive than they very often are and to this end one can see a channel running along the back of the frame where the cables will be hidden out of view, the channel itself being covered with a 5cm strip of veneered plywood.
As for the support rig, I am in discussion with someone in Germany who may build it for me or alternatively will try and make use of a local precision engineering company. Whilst I had for some time considered making the frame out of oak, which is fairly cheap and plentiful, I wanted a material that would enable me to have a very narrow profile. I wanted to keep the thickness of the mast cross section at no more than 12cm (which will look more like 8-9cm with the bevelled edges I chose to have for the front face). I also wanted a wood sturdy enough to cope with a potential weight of 80-150 kg hanging some distance from the centre of mass of the frame. All in all, oak did not seem to fit these requirements although Russ who is building the LVFrame felt that oak would have been good enough.
In any case, I then came across a beam of Guaiacum (Also known as Lignum Vitae) wood, which is incredibly dense and strong, in fact three times as hard as oak, a very oily wood which also had a beautiful grain that only require the application of danish oil. It is a protected species but I sourced mine from a beam that had been used as part of the structure of a pier used under water for well over 30 years and came out looking that it had been cut yesterday. I am not too sure to what extent I should be concerned about the isolation and resonant free characteristics of the frame in my application, but in any case, the hope is that this wood with its incredible density and therefore greater mass will be more immune to environmental vibrations.
I will upload some pictures in due course as well as some more explanation as to how the frame is made adjustable. As you can see this is work in progress...
Best regards Rakesh
|
|
|
|
|
Posted by Romy the Cat on
10-18-2011
|
fiogf49gjkf0d ....but can you post a sketch of your future frame with horns? I assure you that the images of specific micro-details of constructing without understanding the content of enter project, how horn are related to each other, and how frame will hold them would mean very little for anyone.
The Cat
|
|
|
Posted by oxric on
10-19-2011
|
fiogf49gjkf0d
Below is a sketch of the main frame, that Russ made for me based on our original discussions many months ago, consisting of the support for the UB115 horns and missing some finishing details such as bevelled edges, top end feature, holes for horizontal supporting rods and other adjustability features.
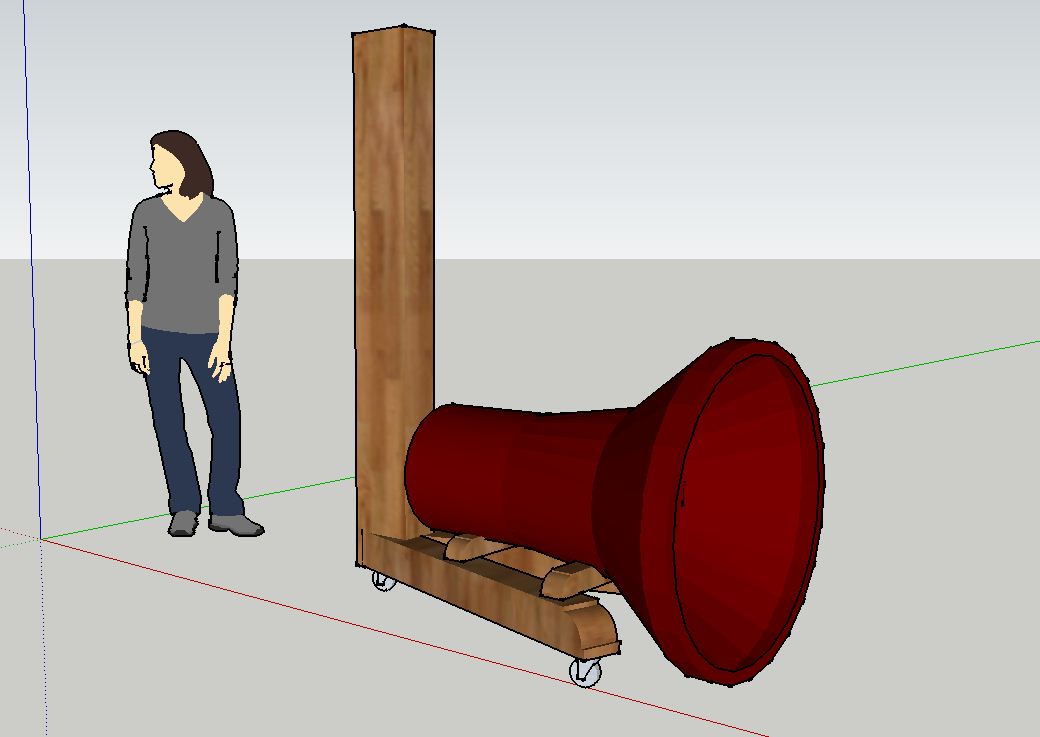
The supporting rig has gone through a number of iterations but the main feature is that it consists of a number of aluminium or steel rods which can be located at different heights as there will be a series of holes at approximately 15cm intervals, from which vertical threaded rods will allow further adjustments in both the vertical and horizontal plane. I will make another sketch once I know who will build it for me and what design the builder will be comfortable with.
Best regards Rakesh
|
|
|
Posted by Romy the Cat on
10-19-2011
|
fiogf49gjkf0d Very good. One thing that I would like to note that you might not consider now as you have no practical experience with those things for now. This thing is a personal preference and has no impact to sound.
I personally prefer when I sit in my listening spot and look at the speaker then I would like do NOT see the mechanisms the hold the speakers. If I see the harness that holds the channels then it gives to me some overly utilitarian feeling. It always likes some “glory” of American architecture when they build beautiful houses with magnificence façade and in the middle of everything they run an ugly fire escape latter that made the whole appurtenance very functional but esthetically unpleasant. For sure no one argue the need of fire escape but you what I mean.
So, I personally prefer do not see any side-element of frame from listening spot. This is why I criticized Jessie’s Fundamentals Hors that in my view had too much harness visible. If you look at the speaker from 45 degree then it will look like it flying in air – very cool appurtenance. If you look at the image below then you see that there is no frame visible on side:
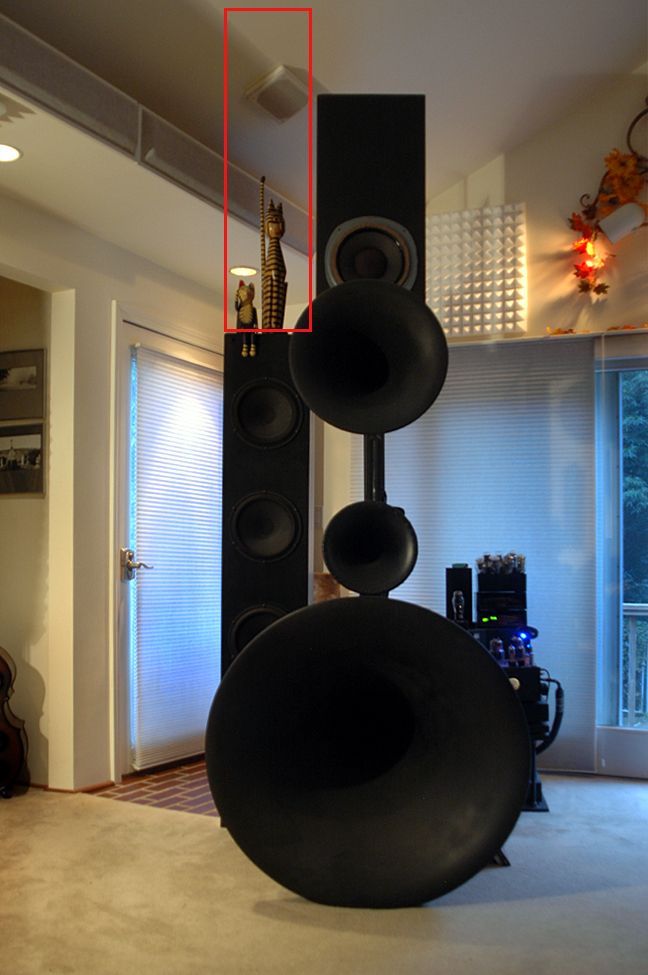 Looking at your drawing I am afraid that the left of the right legs will be sticking out of the perimeter of the upperbass horn. There is nothing to be afraid; it might be not a big deal for you. You might also to moderate the length of the legs make them to hide behind the horn. Anyhow, you might think about it now as now it is very cheap to adjust. Again, it is my preferences and criteria and they might mean nothing to you.
Also, if you keep the horns unfinished then the selection of wood frame is justifiable and it will give whole woody look and feel. Still I would vote for metal frame. It is cheaper to make (MUCH cheaper!), it is much stronger, it will not bend and wave with time, you can use much more pressure to hold to it and the most important it might be significantly thinner to care the same mass.
Rgs, The Cat
|
|
|
Posted by oxric on
10-20-2011
|
fiogf49gjkf0d
From ghoulies and ghosties And long-leggedy beasties And things that go bump in the night, Good Lord, deliver us!
Anon
Romy the Cat wrote: |
I personally prefer when I sit in my listening spot and look at the speaker then I would like do NOT see the mechanisms the hold the speakers... If I see the harness that holds the channels then it gives to me some overly utilitarian feeling.
|
|
I agree. Without being a designer, I like forms to be not only functional and elegant but additionally not to clash and this can happen when you have a random hotchpotch of very different geometric elements, as would be the case with the elongated vertical lines and harsh angular structure of the frame and the beautiful circular shapes of the horns.
Romy the Cat wrote: |
Looking at your drawing I am afraid that the left of the right legs will be sticking out of the perimeter of the upperbass horn. There is nothing to be afraid; it might be not a big deal for you. You might also to moderate the length of the legs make them to hide behind the horn. Anyhow, you might think about it now as now it is very cheap to adjust. Again, it is my preferences and criteria and they might mean nothing to you.
|
|
Whilst your preferences are your own, and have little sway on mine, I had specified quite a long time ago that the legs (and castor wheels) should be invisible from the listening position. You spotted quite correctly though that although recessed behind the horns that the legs were splayed at an angle that would make them visible in part. I had a chat with Russ and this is being addressed by reducing the angle. Thanks for noting this as I had not realised this immediately from looking at the pictures as I ought to have done.
Romy the Cat wrote: |
Also, if you keep the horns unfinished then the selection of wood frame is justifiable and it will give whole woody look and feel.
|
|
I sort of agree with you but I would have too many varying finishes across the three-four channels. These four channels need to be all finished in the same manner and that means that they must be painted. At the moment, a dark bordeaux red is the colour of choice, to suit the furniture and wall colour of the room and the rich red colour of wine, being as we are, located at the heart of the Alsatian Wine Road. As an added bonus, that dark red colour seems to go quite well with the beautiful grain of the Lignum Vitae timber.
Romy the Cat wrote: |
Also, if you keep the horns unfinished then the selection of wood frame is justifiable and it will give whole woody look and feel. Still I would vote for metal frame. It is cheaper to make (MUCH cheaper!), it is much stronger, it will not bend and wave with time, you can use much more pressure to hold to it and the most important it might be significantly thinner to care the same mass.
Rgs, The Cat |
|
You are right. I would advise anyone going down this route to use a metal frame for the reasons you have mentioned. I however find natural wood very soothing and just keeping a sample of that Lignum Vitae timber atop my very modern Ligne Roset Yo-Yo table provides me with a tactile and sensory experience that bare metal could never replicate. As far as strength is concerned, for the application we have in mind, whilst other woods might have posed difficulties, the janka hardness rating of Lignum Vitae susggests that this is a non-issue
http://en.wikipedia.org/wiki/Janka_hardness_test
Of more importance to me are the resonance frequency and sensitivity to environmental vibrations of steel especially in a monopod configuration. With my design, I cannot avoid the problem completely myself as the supporting rig will be made of solid aluminium bars but the frame and rubber castor wheels should provide a fair degree of isolation.Maybe I am worrying about nothing, but as you quite rightly point out, not having any practical experience of such a set-up, I am erring on the side of caution, and probably am in the process of avoiding imaginary evils whilst falling prey of the very real ones that I cannot see for now.
Best regards Rakesh
|
|
|
Posted by Romy the Cat on
10-21-2011
|
fiogf49gjkf0d oxric wrote: | Of more importance to me are the resonance frequency and sensitivity to environmental vibrations of steel especially in a monopod configuration. |
|
Well, the resonance frequency of frame is the subject sucked out of nowhere. I can’t not even begin to tell how irrelevant it is. BTW, if, a big if, you feel that it is important to you than metal frame has much more flexibility to moderate resonance frequency. A 3 by 4 metal frame can care humongous wait, including bend and if you willing to tinkle with resonance frequency then you can fill the hollow 3 by 4 metal frame with sand of even with led shots. Warn you: when you put all your horns on the frame it will be so heavy that you will be laughing that you ever thigh about resonance frequency. The few grams of decagrams in those channels will be nowhere close to be able to excite the mass of the entire assembly. Sure, it is a free country and you might do whatever you wish, you might even initiate a group resonance frequency calculation, but I think that it has absolutely no practical meaning.
One more thing. You and Jessie and a few other folks that I have seen make the bottom of what I call “Horns Island” (in analogy with the air carrier deck) with wheels. This is certainly a very good decision BUT only if you not doing to use carpet. You see, the wheels work on carper if they are relatively large, let say 4-5 inch. It is how they are depicted at your sketch. However, you might discover in future that as you install your speaker in final position then you do not need the wheels anymore. Furthermore, in context of the permanently installed Horns Island the wheels might be a bit too utilitarian not to say ugly. You might not be able to remove them as your midbass will sink too deep. So, you need to devise some kind of idea that would take advantage of the wheels and then, after the final position is find would allow you to remove the wheels one by one, preserving the speaker found final location. I wish I thought about it when I was designing my Macondo frame….
The Cat
|
|
|
Posted by oxric on
10-21-2011
|
fiogf49gjkf0d Romy the Cat wrote: |
Well, the resonance frequency of frame is the subject sucked out of nowhere. I can’t not even begin to tell how irrelevant it is.
|
|
You are probably right. Obviously not having lived in earnest with any multi-way horn system, let alone a "horns-island" as you call it, and having instead lived with several speakers whose enclosures were clearly ill-conceived, I was thinking of these horns acting like pendulums by picking up vibrations from the ground and oscillating...I just do not know.
Romy the Cat wrote: |
One more thing. You and Jessie and a few other folks that I have seen make the bottom of what I call “Horns Island” (in analogy with the air carrier deck) with wheels. This is certainly a very good decision BUT only if you not doing to use carpet. You see, the wheels work on carper if they are relatively large, let say 4-5 inch. It is how they are depicted at your sketch. However, you might discover in future that as you install your speaker in final position then you do not need the wheels anymore. Furthermore, in context of the permanently installed Horns Island the wheels might be a bit too utilitarian not to say ugly. You might not be able to remove them as your midbass will sink too deep. So, you need to devise some kind of idea that would take advantage of the wheels and then, after the final position is find would allow you to remove the wheels one by one, preserving the speaker found final location. I wish I thought about it when I was designing my Macondo frame….
The Cat |
|
I have solid wood flooring in the room with a rug thrown in front of the horns so the operation of the wheels should not be unduly hindered. As to aesthetics, this is a rather thorny issue to which I do not have a satisfactory solution. I have thought about this for some time and considered putting in some sort of skirt around the edge of the base to hide the wheels. I do not like the appearance of it. I thought of trying to find some castor wheels with wooden accents and there may be some I have found that will be not too dreadful looking. In any case, I will have the base made so that the wheels could be removed and replaced with some legs so the overall height of the frame and supported horns are maintained once the final position is found. It would be great if these legs would complement the design of the frame. Or I could just baptise the castor wheels "rotae vitae," an empty latin phrase will go a long way to hide many a sin.
A slightly crazy idea I have had in terms of the design of the frame was to incorporate some sort of discrete but fairly precise calibration of the supporting rods so I would be able to keep note of the relative position of the horns and tweeter as they are moved in position, as well as a device that would enable me to instantly measure distances to the listening position from the relevant locations on the drivers, with separate digital displays thrown in for good measure. I wish Jessie lived not too far from here; he would come up with some masterful solution in return for some bottles of Cremants.
Best regards Rakesh
|
|
|
Posted by Romy the Cat on
10-22-2011
|
fiogf49gjkf0d Well, I still am not thrilled with this frame. Not that I have to be but in my view this frame has some potential to be problematic. I am not a structural engineer and I might be wrong but this is the problem how I see it. Wood is a strong material and your frame use some kind of stronger wood. That is fine. However is you look at the height of vertical poll and if you attach it 3 more horns then you will understand that the virtual poll of the frame will have a lot of forward puling momentum and all this momentum will be applied to less than one sq feet surface between the frame’s legs and the vertical poll. Even if you glue it you have no room in there to use powerful bolts to hold the things together. If you drive some very deep studs into the poll then it might do but studs will have metal tightening only from one side. So, if you insist to use wood then I would like very much to see a metal triangular plates screw to the wood from both sides of the poll with good 25-30’ extension along the legs. This way the rocking of the frame will not weaken the vertical poll.
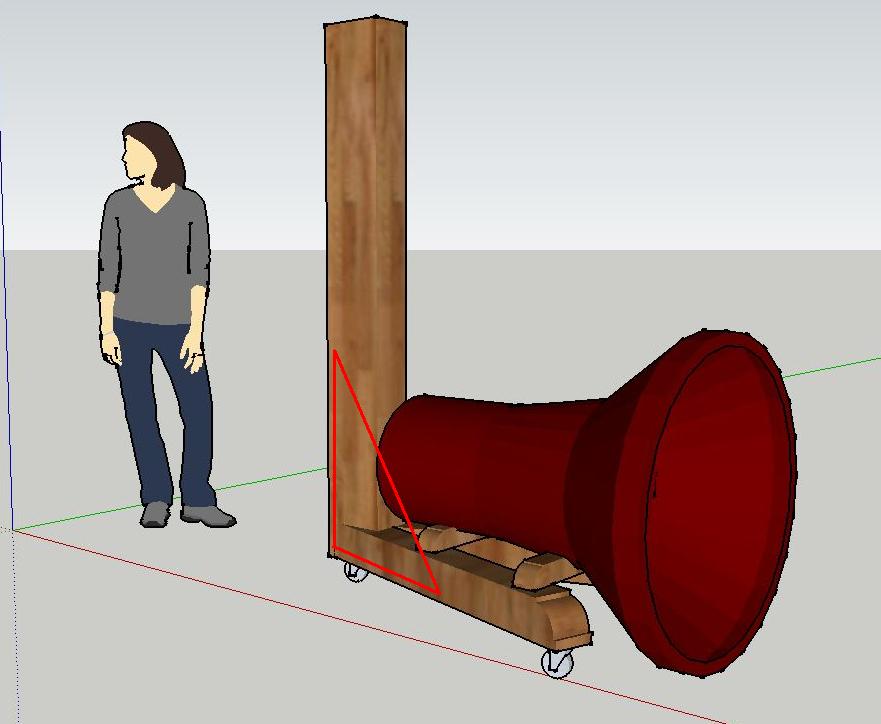
I have those ribs of stiffens and in my estimation they are mandatory for frame of this type.
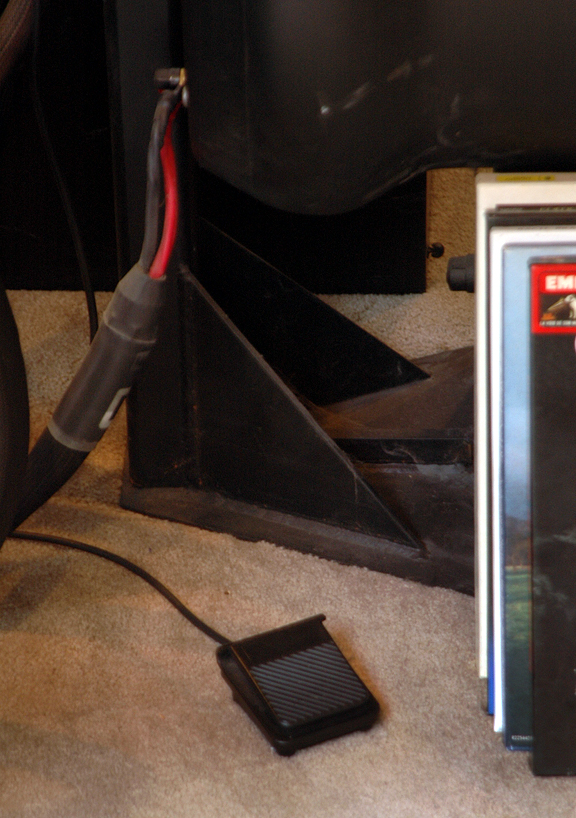
The Cat
|
|